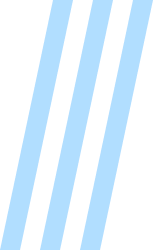
お客様のご要望に的確に答える製品を生産するために、当社のエンジニアがお客様の近くで設計を行っています。お客様と密接な打ち合わせを行うことで、お客様が求める仕様や機能、耐久性などを実現することはもちろん、製造部門と連携を取って、製造現場での「作りやすさ」まで考えた図面を描きます。
数年後に世の中に出る新車に搭載するための部品開発・設計はもちろん、将来を見据えたリサーチ段階の開発にも取り組んでいます。当社からの提案が採用された大きな事例としては、米国において、従来は12年間保証していたフューエルフィラーパイプが、規制が変わることで15年保証する必要が出てきた際、パイプを鉄製からステンレス製に変更し、カチオン電着塗装を行うことで、耐久性を高めることに成功しました。この他にも、ハイブリッドカーや燃料電池車・電気自動車向けに軽量化のため、鉄から異種材料に変える取り組みにも挑戦しています。このように、当社が持つコア技術や蓄積してきたノウハウを活かして、お客様に積極的に提案を行うケースも増えています。
小島工場には研究棟があり、ここでは振動試験や荷重による疲労のチェック、CAEを使った強度解析などを行い、お客様が求めている条件を満たす製品の開発に貢献しています。
プレス加工やパイプ加工では、鉄材だけでなく、ステンレスやアルミニウムをはじめ様々な素材を使用しますので、それぞれの特性や製品に求められる仕様に合わせた最適な金型・治具・加工設備を自社で設計・製作しています。
また、当社の主力製品であるステアリングハンガービームは、加工したパイプに様々な付属部品が数多く取り付けられるため、溶接する時の熱影響を考慮して、要求精度を保証するなど、当社独自のノウハウも折り込んでいます。