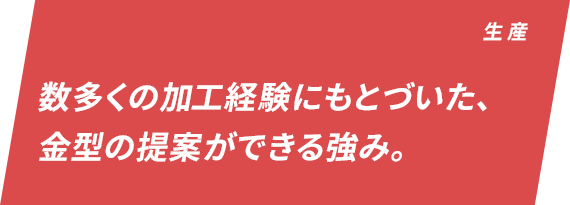
6年間開発課に所属した後、生産本部に異動し、今は、量産を行うためのプレス金型の手配をしています。製品の形状や機能を考えた上で、最適な金型を金型メーカーに「こういう仕様で作って欲しい」と依頼し、量産現場に引き渡すまで推進することが、私の仕事になります。担当しているのは主に順送プレス機で使うための金型。順送プレス金型は帯状になった金属の板を順に送り出し、10〜20工程で成型部品を作る金型なので、長いことが特徴です。また、自分で金型を設計から量産引渡しまで一括で手掛けた事も有り最大で長さが2.5メートルというサイズの順送金型製作も経験しました。
一番印象に残っているのは、アルミニウムの薄板(厚さ0.4〜0.6ミリ)をプレスしてマフラーパイプとボデーの間の遮熱板を量産するための金型です。アルミニウムは鉄と違い、紙と同じで伸びない素材のため、金型の形状を間違えると亀裂ができてしまったり、しわができてしまいます。そういう不具合が発生しないように、時間をかけて何度もトライ&エラーを行いながら、仕上げていきました。苦労が多かった分、完成した時の感動が大きかったことを憶えています。その金型は、今は日本だけでなく、インドの工場でも使われています。
作る部品によって、金型の形状も、注意すべき点も、毎回違ってきます。営業が持ってきた情報をもとにして、まず「プレスで作ることができるのか」の検討から始まり、どんな材質の金属板を加工し、どんな工程にするのか、また、金型の大きさはどれくらいになるか等を考えて、お客様に出すコストを算出します。お客様の所にいる当社のゲストエンジニアから「この部品を作れますか?」という問い合わせが来ることもあるので、その質問に応えることも私の仕事です。また、お客様から言われた通りに作ればいいというわけではありません。製作の実現性を考慮して「ここの修正を検討してください」とゲストエンジニアに交渉してもらうこともあれば、「ここをこう変えるとコストダウンできます」と、私の方から提案することもあります。そうした提案が当社に対する信頼につながっていきますから、常に最適な金型になるように知恵を絞っています。生産をする時にトラブルがなく、作りやすく、高い品質の製品を低コストで作ることができる金型を考えることが、私の理想です。
当社は新しい意見や斬新なアイデアを受け入れてくれる風土がありますから、積極的に提案するようにしています。自分の考えが採用されて、より良い製品作りに貢献できることが、私の仕事の面白さです。